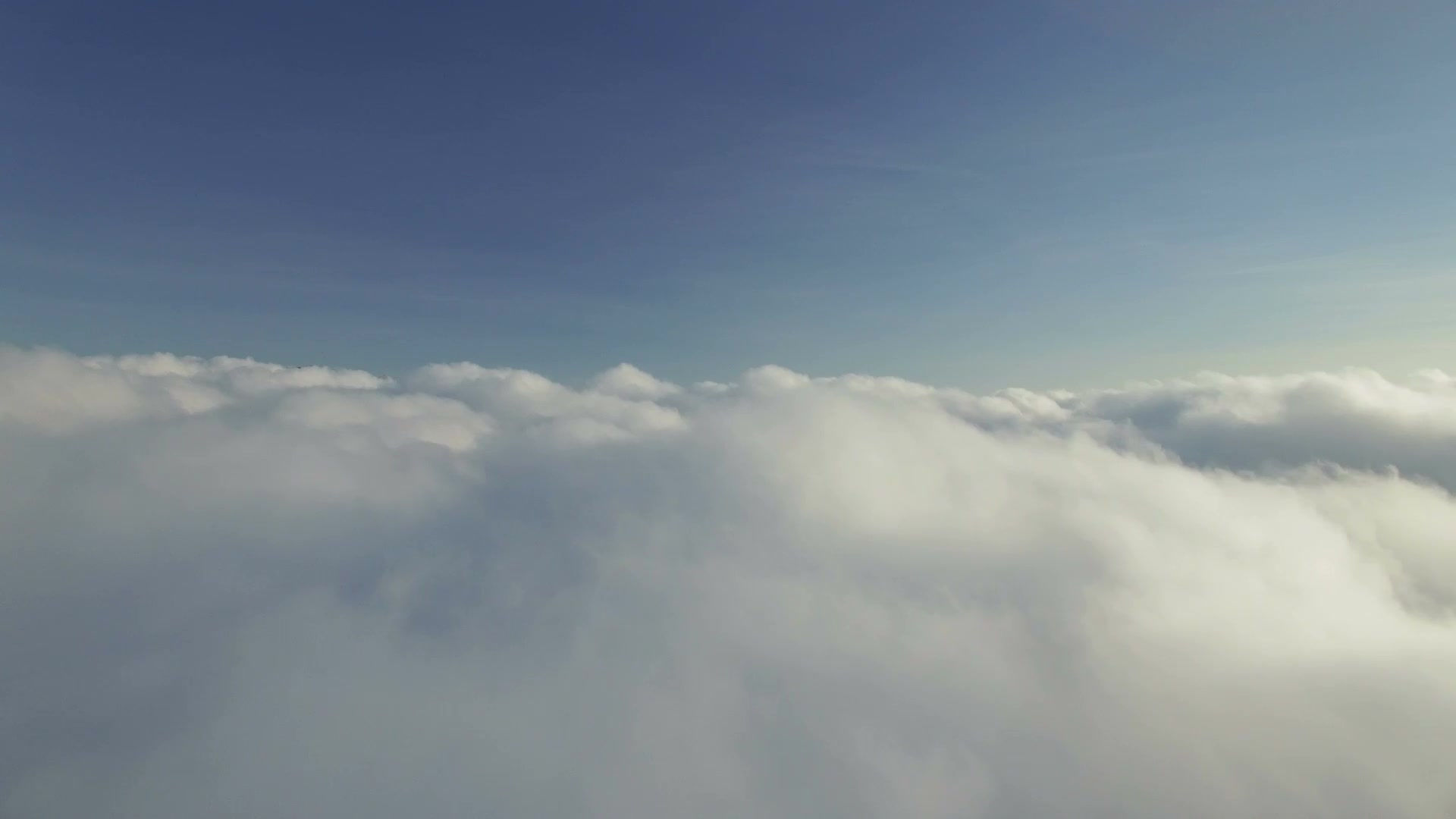
WE ARE LAUNCHING OUR WEBSITE SOON.
CNC Machining.
1. The cnc processing and production process is not concentrated enough and too scattered
The root cause of this problem depends on the fear of being cumbersome, the programming is simple and the operation is simple, often want to use the same knife to finish machining, it is easy to adjust the tool setting when operating the machine, and I am used to the general simple machining, which produces the shape of the product. Tolerances are not easy to ensure, and productivity cannot be fully utilized effectively. Therefore, CNC machining technology operators or machine operators should carry out more study of theoretical knowledge of all-round CNC machine tool machining. Reasonable processing technology design and not too scattered will greatly save time and effort, improve production efficiency and increase production capacity.
2. The CNC processing order lacks rationality and logic
Often some cnc processing operators allocate processing procedures extremely unreasonably, CNC machine processing, effective selection and use of main drilling parameters, etc., in this way, quality and productivity can be improved. If the setting and wrong operation, it will often lead to problems such as overshoot when returning to zero and contusion of the machine slide surface due to the excessive speed setting.
Trial operation and program search can also be performed during CNC machining. Make changes to the system when necessary to ensure the accuracy of the system. At the same time, before declaring the program to execute the processing, be sure to run the test run (turn on the power amplifier) through the program flow to avoid collision.
Surface roughness generally depends on the machining process and other factors, such as the friction between the tool and the surface of the part during machining, the plastic deformation of the surface metal when the chips are separated, and the high-frequency vibration in the machining system. The depth, density, shape and texture of marks on the surface of the part also vary depending on the machining technique and the aluminum alloy.
Generally speaking, reducing the surface roughness value will improve the assembly quality of the part, reduce wear and prolong the life of the part, but also increase the processing cost of the part. Therefore, in order to reasonably select the surface roughness value, before processing magnesium-aluminum alloy parts, it is necessary to clarify the role of magnesium-aluminum alloy parts in a specific industry to determine the selection of surface roughness values.
Generally speaking, in principle, a larger surface roughness value is selected on the basis of meeting the technical requirements. Please refer to the following principles for details.
(1) The roughness value of the working surface is less than the roughness value of the non-working surface.
(2) The roughness value of the friction surface is smaller than that of the non-friction surface. The higher the friction speed of the friction surface, the greater the unit pressure, and the higher the stress required for the rolling friction surface is than the required roughness value for the sliding friction surface.
(3) Regarding the clearance fit, the smaller the fitting clearance, the smaller the roughness value; for the interference fit, in order to ensure the firmness and reliability of the fastening strength, the larger the load, the smaller the roughness value required. The roughness value is smaller than that of the interference fit.
Surface roughness plays an important role in aluminum alloy parts and directly affects the quality of the parts. Therefore, choosing the right surface roughness can greatly contribute to prolonging the life of the part. The following cnc manufacturer's editor will discuss the selection method of surface roughness of aluminum alloy parts.